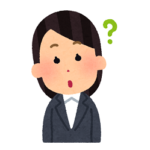
คุณช่วยอธิบายถึงวัตถุประสงค์และแนวทางของ FMEA เพิ่มเติมหน่อยได้มั้ยคะ?
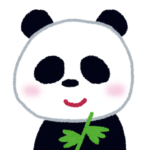
เมื่อพูดถึงการทำ FMEA เราจะนึกถึงสาเหตุของการเกิดความเสียหาย
เนื่องมาจากการเปลี่ยนแปลงของสิ่งเหล่านี้ เช่น อุปกรณ์, บุคคล, เครื่องมือ
หรือสิ่งแวดล้อม เพราะถ้าหากต้นเหตุเปลี่ยน ผลลัพธ์ก็จะเปลี่ยนไปด้วย
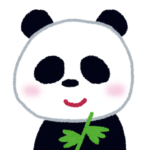
กระบวนการทำงานของ FMEA จะประเมินสาเหตุที่ทำให้เกิดความเสียหายนั่นคือ ลักษณะของความเสียหาย (Failure mode) และ ผลกระทบของความเสียหาย (effect of failure mode) เพื่อป้องกันการทำให้เกิดปัญหา
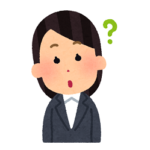
ความแตกต่างระหว่าง “Failure mode (ลักษณะของความเสียหาย)” และ
“Failure (ความเสียหาย)” คืออะไร?
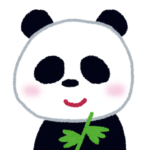
“Failure mode (ลักษณะของความเสียหาย)” หมายถึง ลักษณะการเกิดความเสียหายของแต่ละรายการ “Failure (ความเสียหาย)” หมายถึง ความเสียหายของฟังก์ชั่น
ตัวอย่างด้านล่าง:
“Failure mode (ลักษณะของความเสียหาย)” => “Failure (ความเสียหาย)”: สายเคเบิลไม่สามารถเชื่อมต่อ => มอเตอร์จึงไม่สามารถใช้งานได้
“Failure mode (ลักษณะของความเสียหาย)” => “Failure (ความเสียหาย)“: รถยางแบน => ขับรถไม่ได้
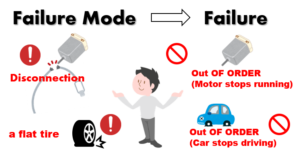
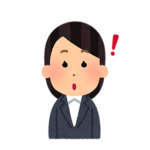
อ่อ เข้าใจแล้วค่ะ
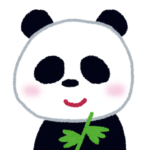
ในอุตสาหกรรมการผลิต FMEA มี 2 ชนิดด้วยกัน คือ
1. Design-FMEA (DFMEA, การออกแบบ FMEA) และ
2. Process-FMEA (PFMEA, กระบวนการผลิต FMEA).
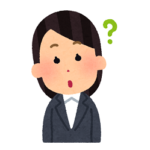
แล้วอะไรคือความแตกต่างระหว่าง Design-FMEA(DFMEA, การออกแบบ FMEA) และ
Process-FMEA(PFMEA, กระบวนการผลิต FMEA) กันนะ?
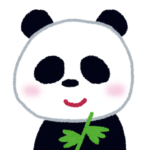
- Design-FMEA (DFMEA, การออกแบบ FMEA): เกี่ยวกับการออกแบบ
- Process-FMEA (PFMEA, กระบวนการผลิต FMEA): เกี่ยวกับกระบวนการผลิต
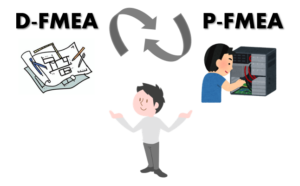
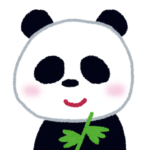
เมื่อเราผลิตสินค้า เราจำเป็นต้องพิจารณาถึงลักษณะของความเสียหายทั้งกระบวนการออกแบบและการผลิต ซึ่งเป็นส่วนสำคัญในการเชื่อมต่อของ DFMEA และ PFMEA.
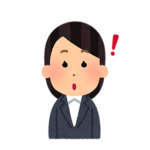
เข้าใจแล้วค่ะว่า FMEA เป็นเครื่องมือที่ช่วยเพิ่มความน่าเชื่อถือในการออกแบบและการผลิตสินค้า
ซึ่งจะช่วยลดการเกิดปัญหาและความเสียหายในการผลิตสินค้า
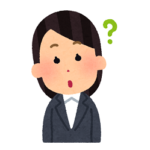
งั้นช่วยบอกวิธีการทำ FMEA หน่อยได้มั้ยคะ?
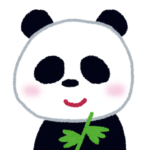
ในการทำ FMEA เราจะประเมินค่าลำดับความสำคัญของความเสี่ยง โดยผลลัพธ์ของค่า
Severity (ความรุนแรง), Frequency (โอกาสในการเกิด) และ Detection (การตรวจหา)
ซึ่งผลลัพธ์ที่เกิดขึ้นจะช่วยให้เราจัดลำดับความเสี่ยง
*RPN : Risk Priority Number (ค่าลำดับความสำคัญของความเสี่ยง)
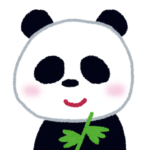
① กรอกข้อมูล “Failure mode” ลักษณะการเกิดความเสียหายของแต่ละรายการ
② กรอกผลกระทบของ “Failure mode” ที่เกิดขึ้นกับรายการสินค้าและรายชื่อลูกค้า
③ ให้คะแนนความรุนแรงของความเสียหาย (จาก 1 ถึง 10)
④ กรอกอัตราการเกิดความเสียหาย
⑤ ให้คะแนนอัตราการเกิดความเสียหาย (จาก 1 ถึง 10)
⑥ กรอกวิธีการตรวจหาความเสียหาย
⑦ ให้คะแนนวิธีการตรวจหาความเสียหาย (จาก 1 ถึง 10)
⑧ นำตัวเลขจากข้อ 3 ,5 และ 7 มารวมกันจะได้ ค่าลำดับความสำคัญของความเสี่ยง (RPN)
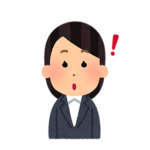
อย่างนี้ เราก็จะสามารถหาค่าลำดับความสำคัญของความเสี่ยง ได้ตามวิธีด้านบน สินะ
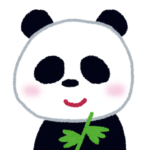
ใช่เลยครับ และหากผลลัพธ์ที่ได้จากขั้นตอนด้านบนมีค่าสูง เราสามารถลดค่าของผลลัพธ์ (RPN)
ได้จากวิธีที่ ⑨ และ ⑩ ดังนี้
⑨ สำหรับชิ้นงานที่มีค่าลำดับความสำคัญของความเสี่ยง RPN สูง
ให้กรอกแผนการพัฒนา ที่จะช่วยลดความเสี่ยง
⑩ คำนวณค่า RPN อีกครั้ง ตามแผนการพัฒนา และหากคะแนน RPN ยังไม่เป็นไปตามเป้าหมาย
เราสามารถกลับไปทำขั้นตอนที่ ⑨ เพื่อผลลัพธ์ที่ดีขึ้นได้
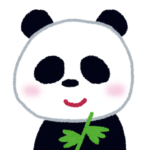
ขั้นตอนที่ ① และ ② มีความสำคัญเป็นอย่างมาก หากกรอกข้อมูลไม่ครบถ้วน ก็จะทำให้ FMEA ไม่มีประสิทธิภาพ
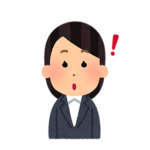
เข้าใจแล้วค่ะ ว่าเราสามารถลดค่าลำดับความสำคัญของความเสี่ยง RPN ใน FMEA ได้ โดยการลดอัตรา “โอกาสเกิด (Frequency)” และ เพิ่มประสิทธิภาพในการตรวจหา”การตรวจหา (Detection)“
**ค่า RPN ยิ่งน้อยยิ่งดี
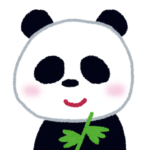
ใช่เลยครับ อย่างไรก็ตาม FMEA ต้องการให้เราตรวจสอบข้อมูลที่เรากรอกเป็นระยะๆ
ตามที่ได้แก้ไขหรือปรับเปลี่ยนข้อมูลในสาเหตุของความเสียหายมันเป็นสิ่งสำคัญที่ลดความเสี่ยง
เพื่อทำการขอการรับรองมาตราฐาน IATF16949 เมื่อเราจะพัฒนาสินค้ารุ่นใหม่
เราสามารถอ้างอิงข้อมูลจากสินค้ารุ่นเก่าเพื่อเป็นต้นแบบในการผลิตสินค้ารุ่นใหม่ได้
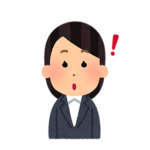
เข้าใจแล้วค่ะ
ในการทำ FMEA อาจเป็นเรื่องที่ดูซับซ้อน แต่หากเราได้เตรียมข้อมูลไว้แล้ว ในครั้งถัดๆไป
เราสามารถนำข้อมูลที่เตรียมไว้มาใช้ในการทำโมเดลของสินค้ารุ่นใหม่ๆ ได้ทันที
โดยไม่ต้องเริ่มต้นใหม่ถูกต้องมั้ยคะ
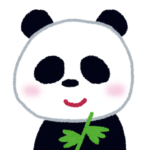
ถูกต้องแล้วครับ งั้นทางเราขอนำเสนอซอฟแวร์ APIS IQ ที่สามารถทำ FMEA และวิเคาระห์ความเสี่ยง
คลิก ที่นี่ เพื่อศึกษา APIS IQ เพิ่มเติมครับ